Thought I’d post a little update while waiting for the delivery of the wheels I ordered, which are needed before I can proceed to assemble the first base section. Delivery is delayed a bit given the current world situation; not entirely unexpected.
I’ve never worked with metals before (apart from spice racks & the like made in high-school shop class), so I’ve been practicing brazing cutoff bits & pieces, taking notes as I go.
Below is a shot of my very first attempt at joining a 3/4″ tube perpendicularly to a 1″ tube. The brazing rod wasn’t melting as I expected it would, so I wound up overheating the piece to the melting point of alu: 1200°F (you can even see a hole burned through the end of the 3/4″ piece). That didn’t work out well, lol. 😀

Subsequent attempts, albeit a bit sloppy, produced better results, as seen in the next pic (view is after I managed to break it).
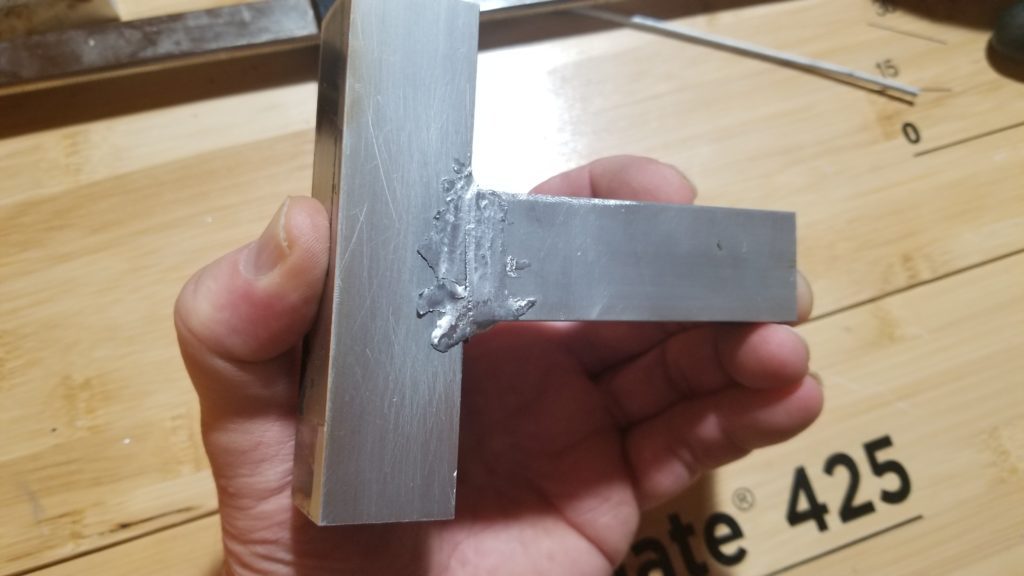
However, by inserting 30″ lengths in each piece as levers and applying a decent amount of angular force, I was able to shear the pieces apart, as seen below.
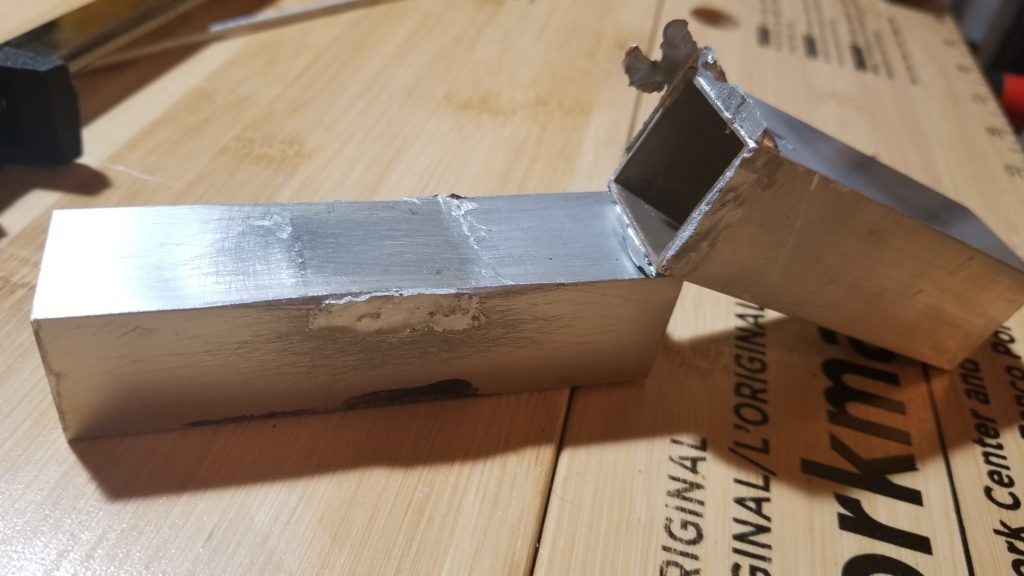
A joint like the one above above would have been perfectly adequate for the trailer floor pieces after some cleaning up. But I’m not 100% confident that would hold up over time with all the jolting the trailer would receive with regular use.
While the brazing material did adhere somewhat to the base stock, we can see that the bond wasn’t as strong as we’d like. Although the image below shows that, upon closer inspection, the aluminum did warp outwards under pressure before the joint failed.
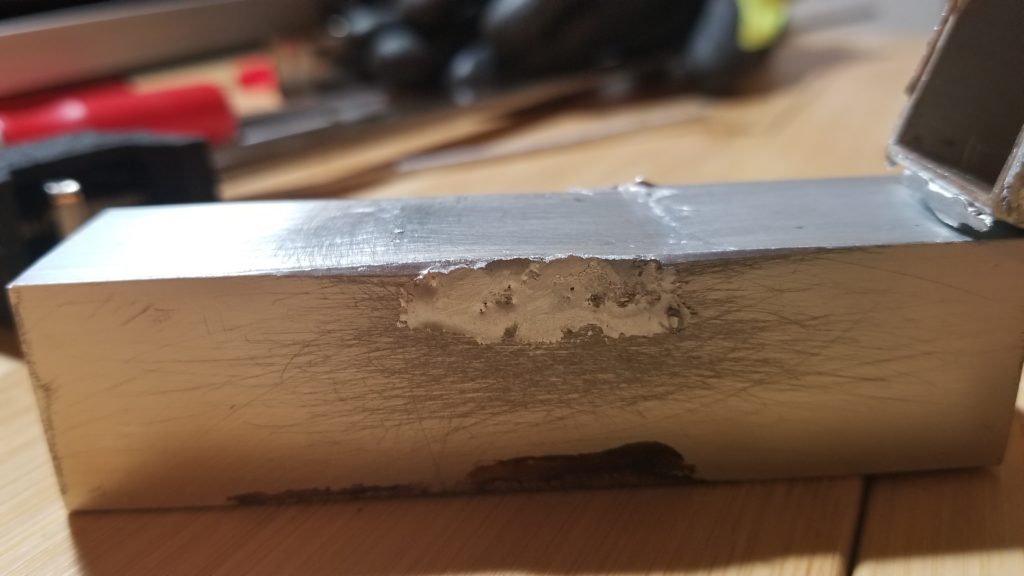
This made me realize that the stainless steel brushes I picked up on the cheap at my local dollar store simply aren’t stiff enough to properly clean & abrade the material. In the images above, you can see the result of trying to use coarse sandpaper to roughen up the surfaces.
Plus, my first failed attempts prompted me to be over-careful to not overheat the aluminum. So I believe I may have simply not heated it enough. Next attempts will surely prove more fruitful… fingers & toes crossed. 😛